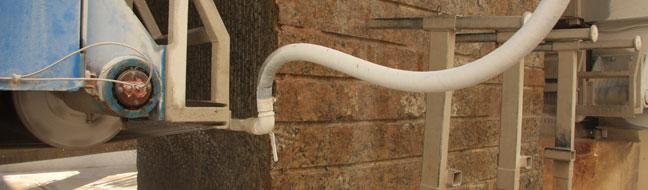
Once blocks of stone reach the processing facility, they are cut down into smaller more manageable pieces. For tile, this means cutting the stone into billets before polishing. For slab materials, this typically means a trip to the gang saw. A gang saw works just like a giant bread slicer, with many adjustable blades that allow for the thickness of the slabs to be adjusted. The gang saw can cut the entire block of stone into slabs at one time. More delicate materials may require the use of a diamond wire saw to gently cut one slab at a time with less trauma to the stone. The most recent technology involves multi-wire gang saws which have the potential speed production on exotic materials exponentially.
After slabs are cut on the gang saw, they are moved one at a time to the polishing line, where they are laid horizontally on a large conveyer type line called a polishing line. There, they pass under polishing heads which begin with very coarse diamond abrasives, and then move to finer and finer grit abrasives, just like sanding wood. Travertine slabs and some marbles, will receive a cementicous or epoxy compound to fill the natural voids of the stone. Part of the way through this line, slabs of granite, marble, and onyx will receive a coating of a resin treatment which will fill in any pits or micro fissures which are inherent to the stone in order to make the final surface easier to clean. Most of the excess resin is removed by further polishing, with only 1% remaining on the finished surface. For materials where the final surface is to be honed, the process will stop with a lower grit abrasive than materials with a polished surface.
For stone that will be processed into tile, long strips of material experience the same polishing process, before being cut to size. Some tiles, especially polished materials, will additionally have a small bevel, or arris, added which will make the final installation look flawless.
At this point the materials are checked for quality and carefully packaged for their long journey. Tiles are packed into boxes and tightly fit into wooden crates that will protect them from bumps along the way. Slabs are bundled together and braced with a wooden framework, custom built to ensure the slabs stay upright during the shipping process. All materials are loaded into standard 20 foot shipping containers and braced to prevent any shifting or movement which could cause damage to the material. Due to the immense weight of stone, many containers are not fully packed, but are loaded to maximum weight limit of 42,000 pounds, or 20 tons.
The journey begins when the container is loaded by massive cranes onto a large ocean vessel. After about four or five weeks at sea, they arrive at US ports. Here the containers are offloaded with cranes, passed through customs, and transferred to rail cars for the trip to the Midwest. The last leg of the journey is a quick trip via tractor trailer from the rail depot to Global Granite & Marble’s door.
|